Compressor Protection
Compressors are the heart of natural gas movement. Compressor protection requires removal of solids and liquids that can cause harmful wear and damage to compressor valves, pistons, and bearings. These damages can lead to hundreds of thousands of dollars in repair cost and lost operations.
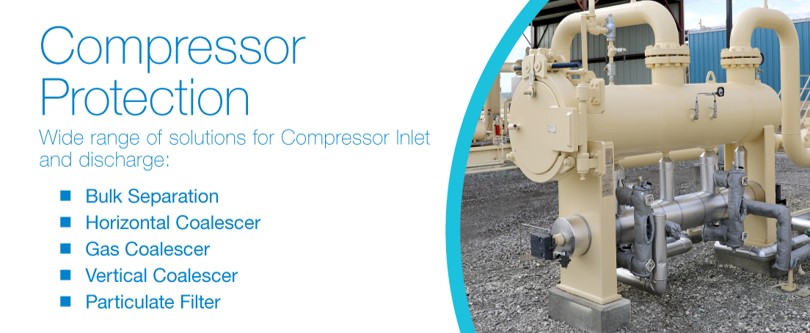
Compressor stations are placed strategically within the gathering and transportation pipeline network to help maintain the pressure and flow of gas to market. They also allow the gas to be rerouted into storage areas during periods of low demand.
Depending on the particular compressor station, its size, sophistication, and other factors, it may or may not be staffed with on-site personnel. Many modern compressor stations can be completely monitored and operated remotely hence the reliability of the filtration equipment is critically important for the smooth functioning of the station.
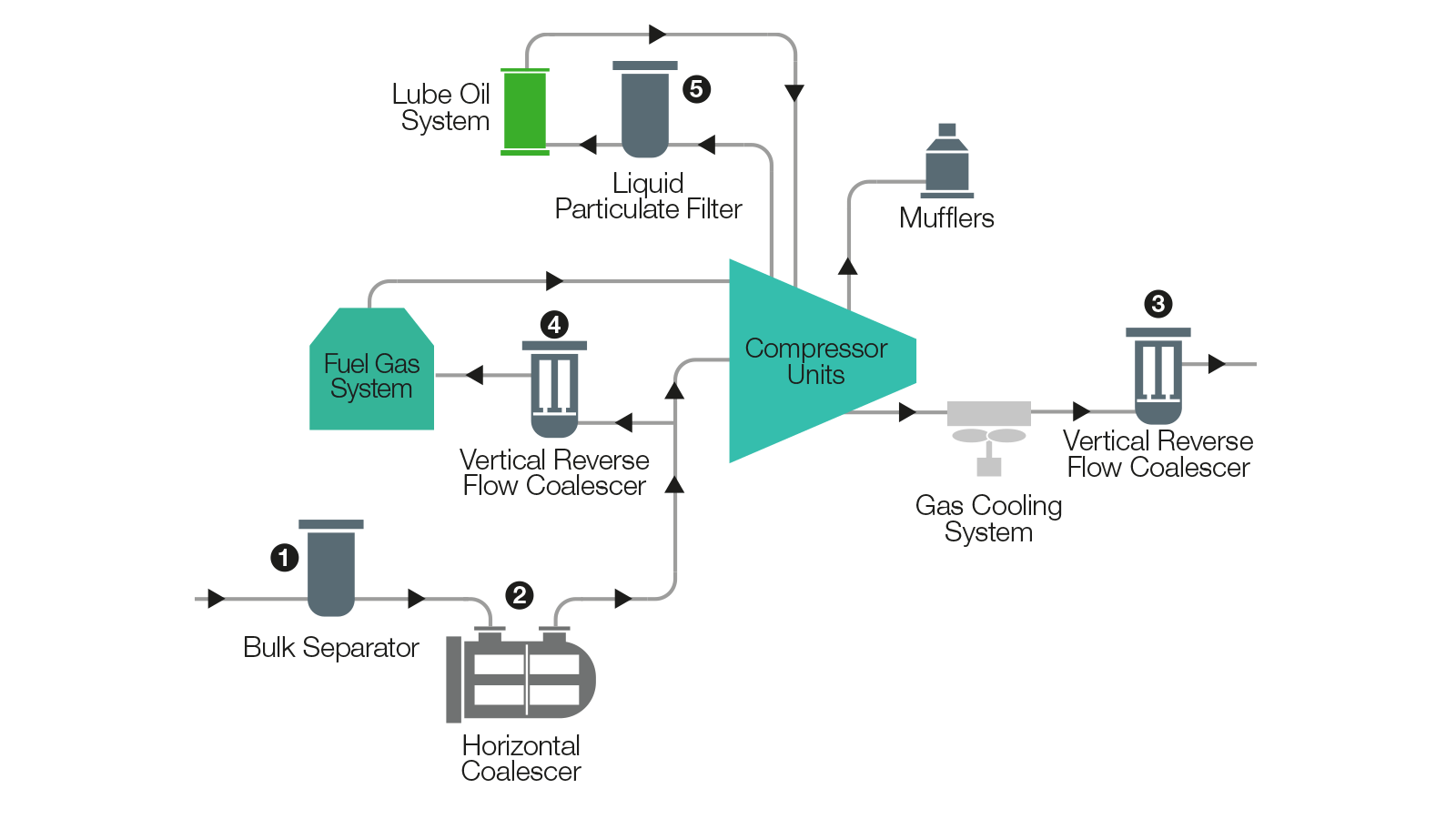
Filter Solution | Filter Purpose | Filter Benefit | |
---|---|---|---|
01 | Bulk Mechanical Scrubber or Separator. | Mechanical separation device designed to handle large slugs of liquids or alleviate high solids and entrained liquid loading from feed gas to primary filtration. | Manages damaging volumes of liquids and provides a predictable maintenance schedule, for primary coalescer, to operations. |
02 | Compressor Inlet Horizontal Coalescer. | Removing solid and liquid contaminants from gas prior to compression. | Efficiently removes difficult, and damaging, low surface tension liquids and shear sensitive Iron Sulfides with low operational costs. |
03 | Compressor discharge gas coalescer with TRI-SHiELD™ filters. | Removing aerosolized low surface tension lubricating oil carryover from exiting compressor gas. | Provide high quality gas for custody transfer, pipeline transmission, or further processing. |
04 | Fuel Gas Filter (vertical coalescer) with TRI-SHiELD™. | Remove solids and aerosols from primary fuel source. | Provide high BTU fuel gas for optimal combustion, reducing NOx emissions and overall fuel consumption. |
05 | Lubricating oil particulate filter using LiquiPleat® technology. | Removing contaminants like wear materials and ash from lube oils. | Maintain ISO cleanliness standard for lube oil. |
Filtration Solutions for Compressor Protection
Jonell systems recommendation is that slugs or bulk removal of liquids be done using SCRUBBERS OR SEPARATORS. If no slugs are expected then proper conditioning of the gas upstream of the compressor should be carried out using a minimum of a filter separator capable of high efficiency 1 micron removal of solids and liquids. For maximum protection of this critical equipment, and lowest Total Cost of Ownership, Jonell Systems recommends the use of horizontal multistage gas coalescer such as the SENTINELTL.
We have a wide range of DEPTH and PLEATED FILTER CARTRIDGES ideally suited for Compressor protection. These include: Twist-LOK, Micro-LOK, Depth LOK, TRI-SHiELD.
Advantages of a Jonell Systems Compressor Protection Filtration Solutions
- Jonell System’s high efficiency highly reliable solutions for compressor protection require minimal maintenance.
- Our Sentinel Horizontal coalescer delivers 10X greater solids capacity, 35X greater liquid capacity, 40% cost savings.
- TRI-SHiELD depth media cartridges for filter separators and coalescers have a significant advantage over other similar cartridges.