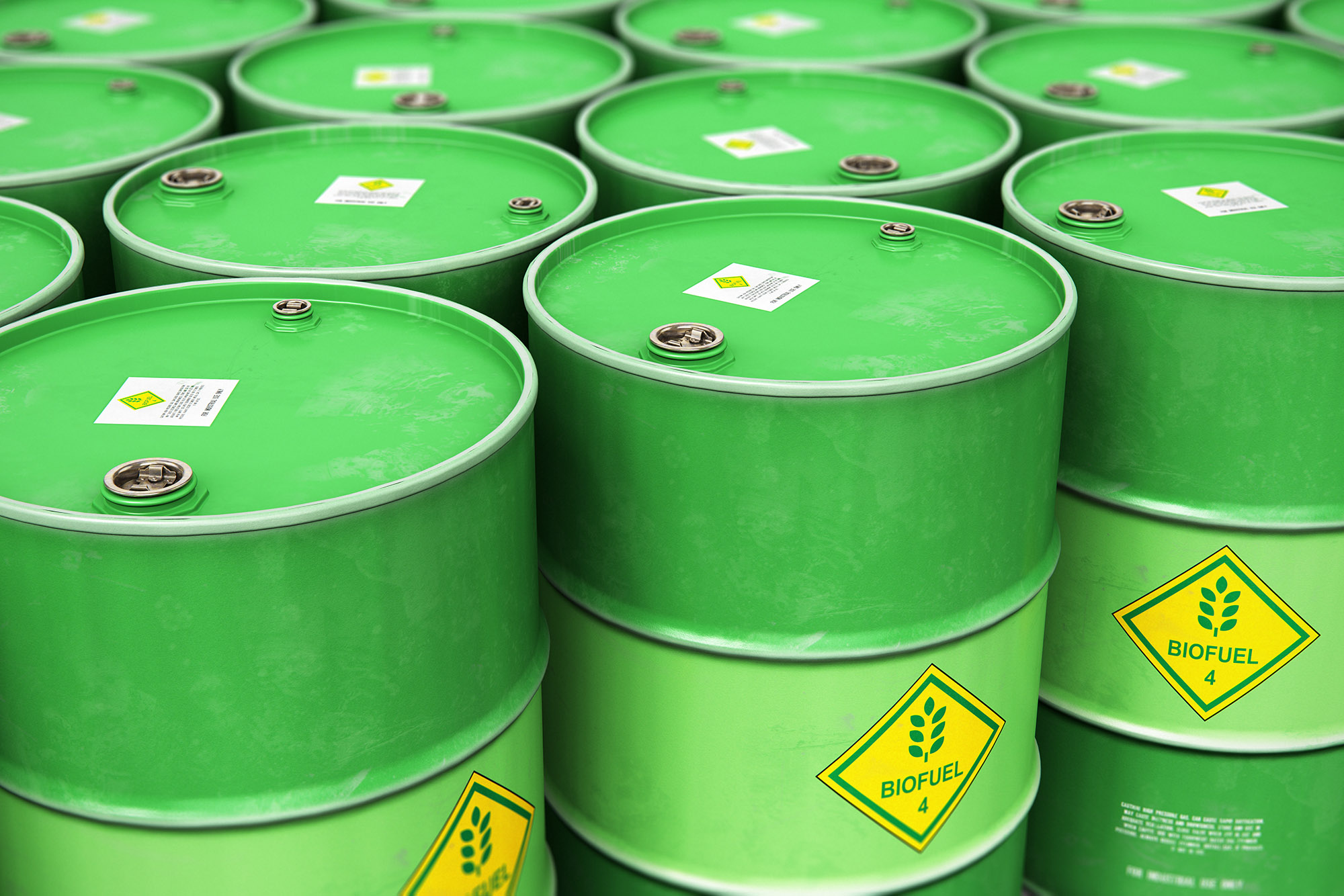
Renewable Hydrocarbon
Biofuels Filtration
As the industry moves towards renewable biofuels produced from various biomass sources, Jonell Systems and Amafilter® have come together to manufacture and deliver feed pre-filtration and post filtration for a wide range of biofuel feedstocks and processes.
Renewable diesel is a drop-in replacement and meets ASTM D975 specification for petroleum diesel whereas Biodiesel is a mono-alkyl ester (meets ASTM D6751) and is approved for blending with petroleum diesel. While the process for producing renewable diesel and biodiesel are not the same, both need feed filtration for further processing.
Renewable Hydrocarbon Biofuels production plants may be stand-alone or co-located at petroleum refineries and may use a variety of processes ranging from traditional hydrotreating to transesterification. With a wide range of filtration solutions, we work with customers to define the most suitable fit for their plant feed filtration process.
Hydrotreating Pre-filtration
Animal fats are attractive feedstocks for biodiesel because their cost is substantially lower than the cost of vegetable oil, and animal fat feedstocks can be made into high-quality renewable diesel. Waste fat from animal carcasses are removed and then made into an oil using a rendering process. Contaminants need to be removed from this oil to provide clean feedstock for the hydrotreater. This is a highly temperature sensitive process which makes this challenging.
Transesterification Pre-filtration
Impurities must be removed from edible oil and cooking oil before it can be converted into biodiesel. The filtration process initiates with the filter system removing fine particles returning the oil to its pure form and ready for transesterification.
Various applications in Renewable Biofuels
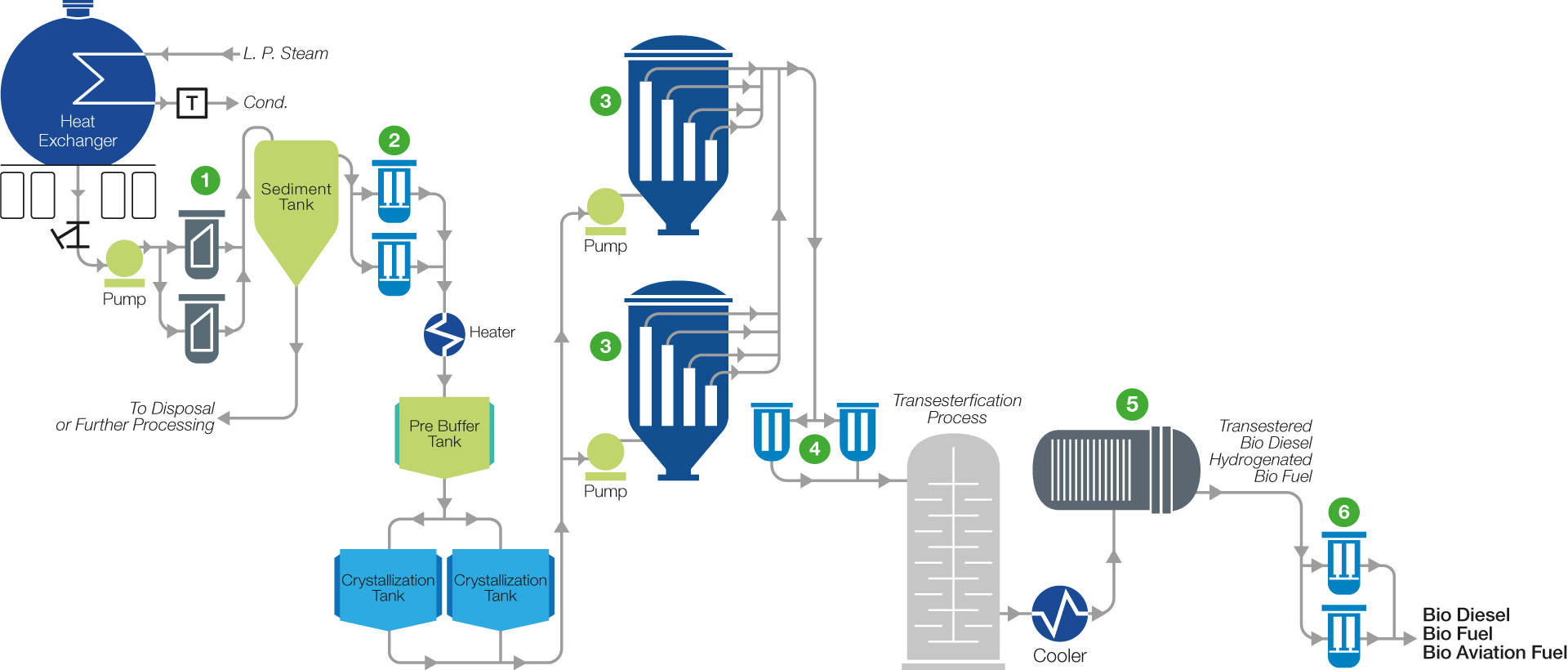
Filter Solution | Filter Location & purpose | Filter benefit | |
---|---|---|---|
1 | Jonell Systems and Amafilter® basket strainers | Removal of large bone meal particulate or other larger contaminants before entering the sediment tank. | Easily remove the large particles from the rendering process. |
2 | Jonell Systems and Amafilter® High flow vessels with pleated bag filter housings | Removal of suspended particulates down to 25 micron after settling in the sediment tank. | Bag filters efficiently remove the next level of particulates. |
3 | Amafilter® Cricketfilter® system | Removal of solid fat & lipids, deodorization and bleaching, polyethylene removal. | The particles collect as cake on the filter and can be removed efficiently. |
4 | Jonell Systems and Amafilter® High flow cartridge filters | Removing fine particulates down to 10 micron before the feed enters the hydrotreater or Transesterification process. | High flow, high efficiency polishing filtration solution to ensure clean feedstock for the hydrotreater. |
5 | Amafilter® Pressure Leaf Filter System | Removal of Haze/sterol particulates down after the feed leaves Hydrotreater or Transesterification process. | The particles collect as cake on the filter and can be removed efficiently. |
6 | Jonell Systems and Amafilter® High flow cartridge filters | Removing fine particulates down after the feed leaves the hydrotreater or Transesterification process. | High flow, high efficiency polishing filtration solution to ensure clean fuel. |
Jonell Systems & Amafilter® renewable biofuels solution advantage
- Jonell Systems & Amafilter® are part of Filtration Group and offer end to end solutions bringing with them the advantage of sourcing the complete filtration solution from one provider.
- In addition, because of the vast range of solutions and custom engineering capabilities, we can recommend and implement the right solution for your process.
- Our solution portfolio includes systems and cartridge based filtration options for a wide range of contaminants from basket strainers, pressure leaf filter systems to high flow solutions.
- These solutions are field proven and have been in use across oil & gas, petrochemical, Food & Beverages and chemical markets.
- High performance solutions reduce the number of maintenance interventions, improve plant efficiency, reduce operational costs and deliver optimal product quality.