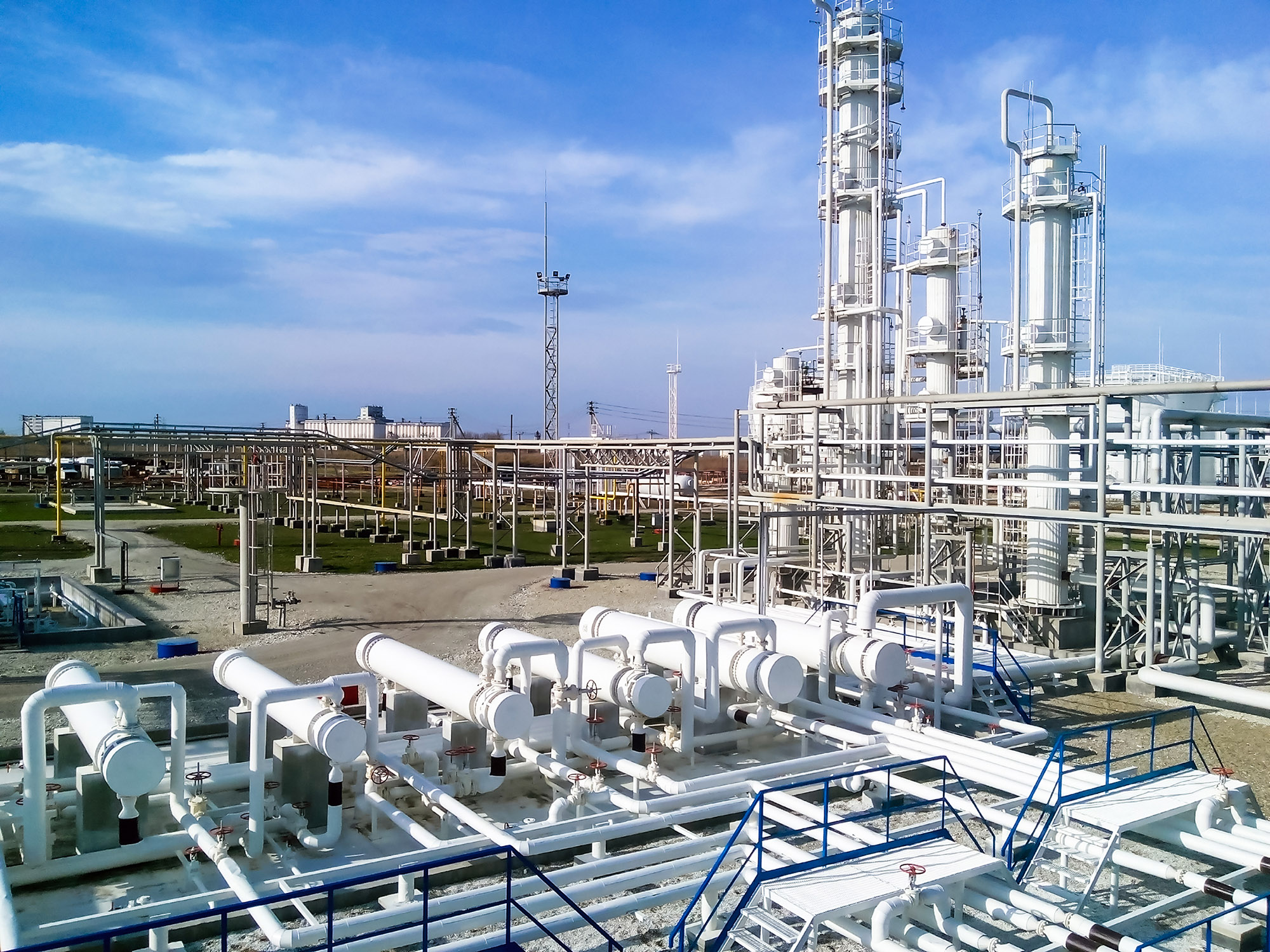
Filtration Optimization in Refineries
Refinery Filtration Optimization
Refineries are being tasked with processing more economical, heavier and sour crudes to maximize profit margins. These opportunity crude oils often possess a broad range of challenging contaminants that can cause plugging and fouling of the key processing units tasked with delivering exacting quality specifications for the final products. These undesirable contaminants can ultimately lead to reductions in processing capacity or even unit shutdowns.
Different types of crude oil yield a different mix of products depending on the crude oil’s natural qualities. Opportunity crude oils such as high acid crudes, heavy-sour crudes and extra-heavy oil produced from oil sands are typically the least expensive on the market, providing refineries with the opportunity to increase profit margins. However, these crudes come with additional concerns such as incompatible crude blends, higher corrosion tendencies and a higher yield of heavy crude fractions.
The filtration requirements for these feeds are determined by the choice of crude blend and the type of processing unit in the refinery, which could be a hydrocracker, hydrotreater or a delayed coker. These considerations affect the contaminants that can be expected as well as determining the optimal location of the filtration solution.
An optimized filtration system protects downstream equipment, improves process uptime, improves process efficiency and reduces the total cost of ownership.
Cost of suboptimal filtration is often increased downtime, increased maintenance on downstream equipment, lower process efficiency and off spec product.
Key filtration problem-solving tools include:
- Feedstock analysis to determine the type of contaminants
- Spent filter analysis to evaluate contaminant loading
- Upstream process change audit to determine the type of filtration and location needs
- Contaminant analysis to choose the right filter media and configuration
Filtration Solution Options for Refinery Filtration Optimization
Filter Cartridge Solution
Based on the location, feed quality and the type of contaminant, one option is to have a cartridge-based filtration solution. There are many media and configuration options available to optimize the removal of solid and semi-solid particulates from the process feed via disposable cartridges. Our wide range of depth and pleated filter cartridges (suitable even for high temperature applications) provide refineries with the optimization capability that is not available with other solution providers.
In addition, our advanced R&D and lab capabilities allow us to design the filter cartridge to specific refinery application challenges to reduce operational cost by increasing cartridge life.
Backwash System
These systems allow for continuous operation to filter particulates from feed streams and protect catalyst beds under the harshest conditions. The solution also can be tailored to the needs of the plant to suit the specific application.
While a cartridge-based system needs regular cartridge change outs, an automated backwash system only needs periodic filter media cleaning and valve maintenance. Disposal of the contaminants should be considered as well when designing a filtration solution. Backwash capacity for an automated backwash system needs to be evaluated, while for a cartridge-based system, the cost of disposal of cartridges and landfill costs should be reviewed.
Hybrid Solutions
There are applications where a combination of solutions can be used to remove particulate from the process feeds to protect the catalyst beds and maintain the run life on catalyst beds at minimal cost. In these solutions a cartridge-based filter is used to pre-filter semi solids to improve the efficiency of the backwashable feed filter.
Conclusion
Ultimately, for a refinery to maximize the profits made possible by opportunity crudes, the design of the filtration solution is critical. Our customized approach of creating a filtration solution to address the specific needs of the customer is how Jonell Systems has helped over 100 refineries worldwide optimize their filtration processes to minimize operating costs and maximize profits.
Talk to us to determine if there are opportunities to reduce the cost of filtration and improve your process reliability and uptime.