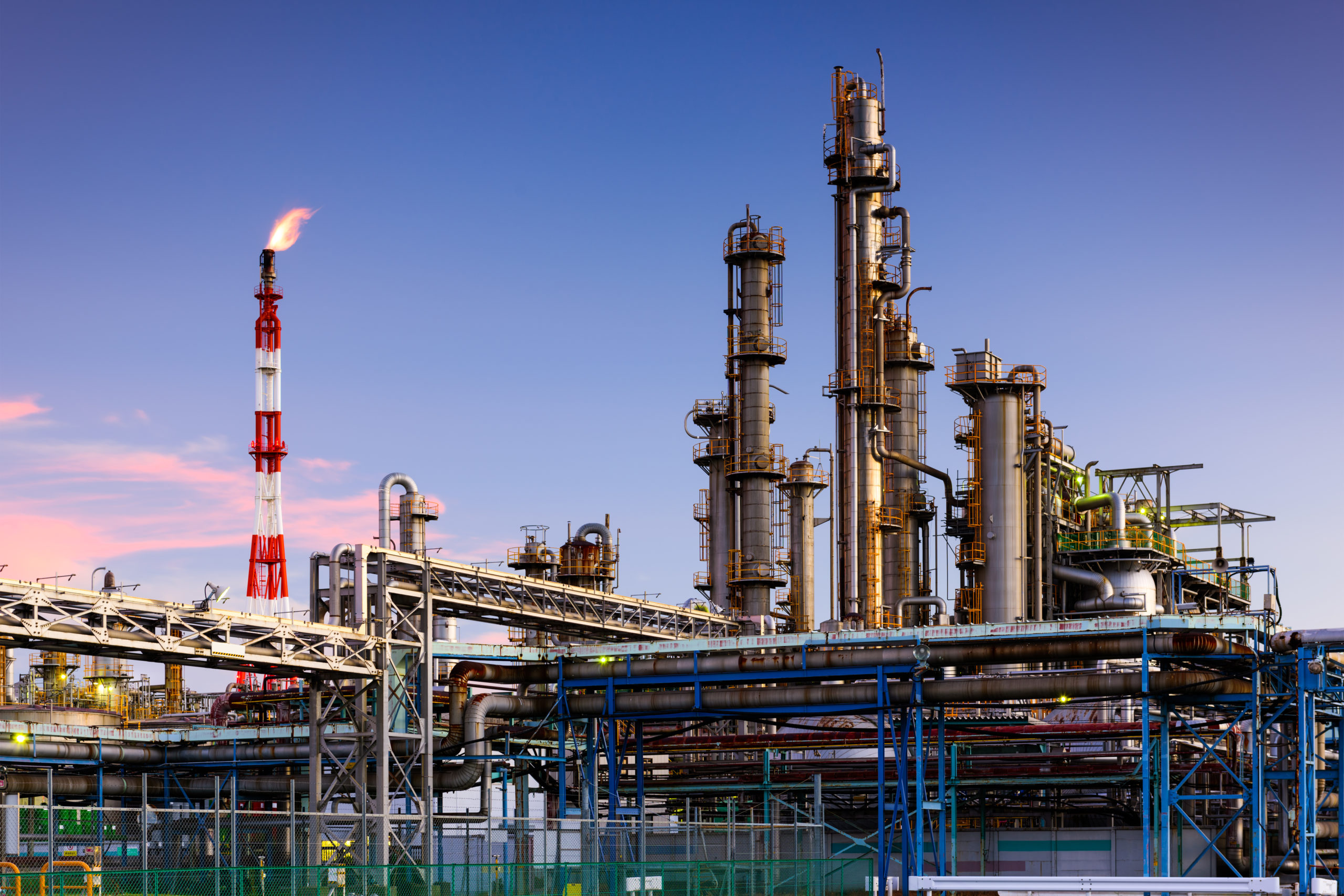
The Evolution of Separation Technology
The Evolution of Separation Technology in the Oil and Gas Industry
Separation technology plays a critical role in the oil and gas industry, ensuring efficient and safe processing of hydrocarbons from wellhead to refinery to consumers. From rudimentary methods to sophisticated systems, this technology’s evolution reflects the industry’s drive for innovation and efficiency.
In the early days of oil production, separation methods were quite primitive, and based almost exclusively on residence time. Techniques such as shotgun separators and hay pack separators were common, but they came with significant limitations such as poor efficiency rates from 1-3%. The need for more efficient and reliable separation processes became evident as the industry grew. Companies such as Facet (one of Jonell’s Filtration Group sister companies!) and Nowata, both founded in 1907, began developing more advanced separation solutions during this period, setting the stage for future innovations.
The period from the 1920s to the 1950s saw significant advancements in separation technology. Innovations included the use of engineered cellulose (hay) and steel gauze, which improved the separation of oil and water, enabling more compact and cost-effective equipment. These developments marked a shift towards more reliable and effective separation technologies. The Filtration Group companies were at the forefront of these changes, continually improving products to meet the industry’s evolving needs.
The 1970s brought about a heightened awareness of environmental issues and the establishment of regulatory bodies like the Environmental Protection Agency (EPA). These regulations forced the energy industry to adopt cleaner and more efficient separation technologies. Collaborations between governmental organizations and private companies led to significant advancements in separation processes, ensuring reduced pollutants and enhanced operational efficiency. During this time, the Filtration Group companies like Facet, Nowata, and Jonell played a crucial role in developing and implementing technologies that complied with these new regulations, ensuring their solutions were both effective and environmentally responsible.
One prominent example of this innovation is the filter-separator, which integrates both filtration and separation processes. This equipment utilizes outside-to-inside flow for initial filtration, capturing larger particles and contaminants, while the coalescing backside ensures liquid droplets are effectively separated. This dual-stage approach improves separation efficiency and extends the equipment’s lifespan by reducing the load on each stage. Jonell, founded in 1987 by John Clarke Sr, has been instrumental in advancing these technologies, providing cutting-edge solutions that meet modern demands.
The 1990s saw the adoption of advanced media, originally developed for healthcare, in the energy sector and marked a significant leap in separation technology with the introduction of high-efficiency, reverse-flow gas coalescers. These coalescers use sophisticated media to capture and agglomerate fine aerosols into larger droplets, which are then separated from the gas stream. This technology ensures that even the smallest contaminants are removed, providing clean gas for downstream processes. However, the order-of-magnitude shift from filter-separators to reverse flow gas coalescers in efficiency came with the drawback of higher consumption and shorter run-times.
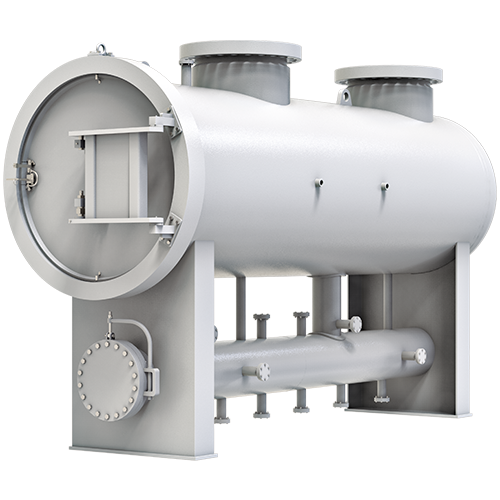
Jonell’s Sentinel TL is an innovative example of modern separation equipment that combines the best features of traditional methods. It utilizes a horizontal configuration, which maximizes gravitational separation and minimizes the footprint of the equipment. This design also includes advanced media for high-efficiency coalescing, ensuring that contaminants are effectively removed from the gas stream. This combination provides the contaminant capacity of filter-separators and the efficiency of gas coalescers, giving a versatility to the Sentinel TL and making it the preferred choice for protecting critical equipment and maintaining operational efficiency in the oil and gas industry.
The added benefit of being able to replace the first and second stage at any time enables users to modify performance, rectify mechanical damage, and inspect the equipment on-site and in hours, compared to fixing mesh and vane second stage components. Jonell Systems continues to lead with its forward-thinking designs and commitment to quality.
The evolution of separation technology has had a profound impact on the oil and gas industry. Modern technologies protect plants, improve operational efficiency, and ensure regulatory compliance. Jonell Systems, formed from the consolidation of Nowata and Jonell, remains a key player in driving these advancements, drawing on our rich legacy and expertise to shape the future of the industry. The journey of separation technology highlights the importance of innovation and environmental responsibility, ensuring the industry can meet its operational and environmental goals. As the industry evolves, the drive for cleaner and more efficient separation technologies will remain a key focus, with Jonell Systems at the forefront of this critical evolution.
Interested in hearing more about Jonell Systems’ innovative filtration technology? Talk to an engineer today.